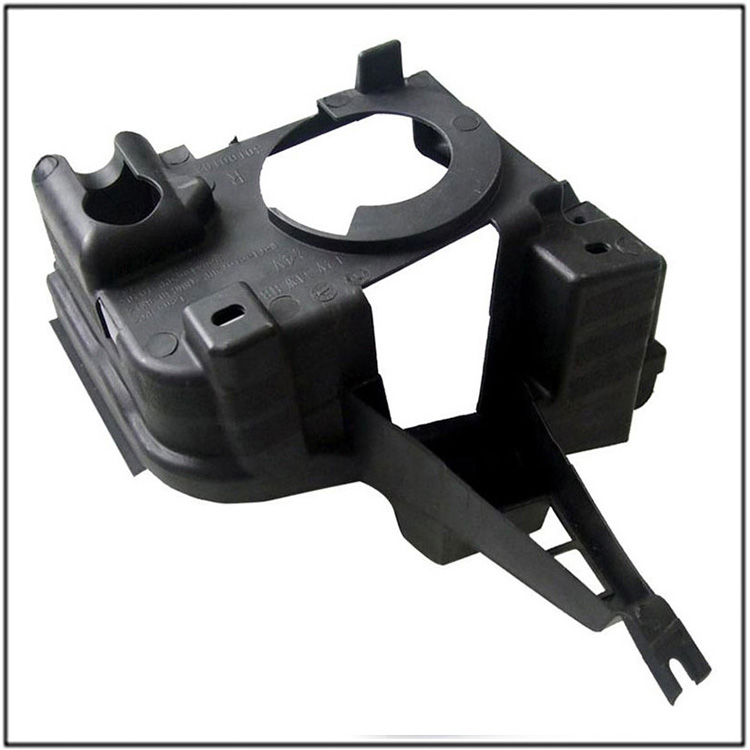
How to Cure The Shrinkage Problem of Injection Molding Parts?
In the latest industry statistics in April 2025, shrinkage defects in injection mold production still account for 23% of quality problems, which is particularly prominent in thick walled products such as automotive components and electronic casings. Shrinkage not only leads to product size deviation, but also triggers chain problems such as stress concentration and appearance depression, directly affecting the service life and market competitiveness of end products. This article will combine the latest industry practices in 2025 to systematically analyze the causes and root causes of shrinkage problems.
The precise control of material shrinkage characteristics is the first hurdle in solving shrinkage. Taking polypropylene (PP) as an example, its shrinkage rate of 1.5% -2.5% is particularly significant in the thick walled region, while the newly released low shrinkage modified PP material (LC-PP) in 2025 can stabilize the shrinkage rate within 0.8% by adding 30% glass fiber and nano nucleating agent. For engineering plastics such as PC/ABS, using narrow distribution resins with a molecular weight distribution index (PDI) below 1.8 can reduce local shrinkage differences caused by uneven molecular chain relaxation.
The dynamic optimization of process parameters is the core means of controlling shrinkage. The pressure curve during the holding phase needs to be accurately matched with the solidification characteristics of the material. The latest developed intelligent holding system can monitor the pressure changes in the mold cavity in real time and automatically compensate for pressure loss before solidification at the front of the melt. The control of melt temperature is equally crucial. Excessive temperature can lead to accelerated degradation and shrinkage, while insufficient temperature can increase flow resistance. By 2025, industry-leading enterprises have widely adopted electromagnetic induction heating systems with a precision of ± 1 ℃, compressing the temperature fluctuation of PA66 material from ± 5 ℃ to ± 0.8 ℃.
The scientific innovation in mold design has brought breakthrough improvements. The 3D printing technology of conformal cooling water channels can increase cooling efficiency by 40%, reducing the difference in cooling rate between thick walled and thin-walled areas to within 15%. The balanced design of the pouring system is equally important. For multi cavity molds, using Moldflow mold flow analysis software to optimize the channel diameter ratio (main runner: branch runner=1.2:1) can control the pressure difference between each cavity within 5%. The refined control of environmental factors is often overlooked. If the moisture content of the raw material exceeds 0.02%, it will cause abnormal shrinkage caused by microbubbles. The 2025 version of the industry standard requires the dew point of the dehumidification dryer to be stable below -40 ℃. The temperature and humidity fluctuations in the molding workshop need to be controlled within the range of ± 2 ℃/± 5% RH, and a full process prevention and control system needs to be established to cure the shrinkage problem.
From intelligent selection of material databases, to intelligent molds equipped with pressure sensors, to online detection systems based on machine vision, industry benchmark enterprises have achieved real-time warning and closed-loop control of shrinkage defects by 2025. With the deep integration of the Materials Genome Project and digital twin technology, future injection molding production will truly achieve "zero defect" manufacturing, opening up new possibilities for precision manufacturing.