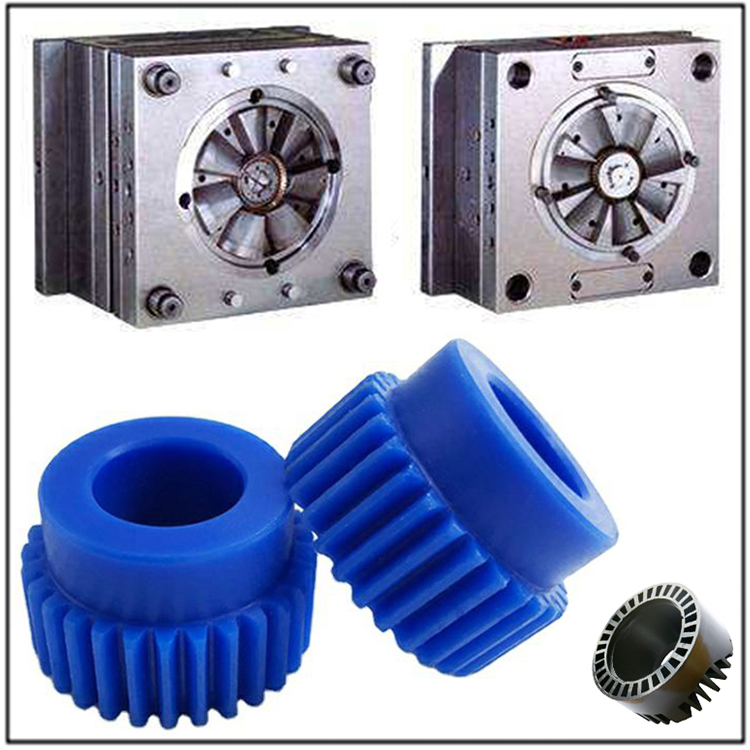
Plastic Mold and Injection Molding Manufactory
What are the 7 key debugging points that plastic mold factories need to master?
In the field of precision manufacturing in 2025, the debugging capability of plastic mold factories directly determines the product qualification rate and production cost. With the popularization of smart factories, the debugging process has shifted from experience driven to data-driven, but 85% of enterprises still experience production delays due to neglecting key details. This article will analyze the core techniques and typical misconceptions of plastic mold debugging.
The bidirectional calibration of temperature control is the primary task. A mold temperature deviation of ± 3 ℃ can cause a 0.2% fluctuation in shrinkage rate. A certain automotive lighting factory has improved the mold temperature uniformity to 98% by introducing an infrared thermal imaging system, resulting in a 40% decrease in product warpage rate. A common misconception is to overly rely on the power of the heating rod and ignore the flow balance of the cooling water circuit. Actual cases have shown that after optimizing the series water channel to a parallel layout, the crystallinity difference of PP material decreased from 15% to 5%.
The dynamic adaptation of pressure parameters determines the quality of molding. By 2025, intelligent injection molding machines will be able to monitor the melt pressure curve in real time, but manual setting of the three-stage holding pressure gradient is still required during debugging. The misconception is that blindly increasing pressure leads to flash. The correct approach is to adjust the pressure tolerance within ± 2MPa by coordinating with the in mold sensor.
The scientific design of exhaust systems is often underestimated. Every 0.01mm ³ of trapped gas will cause a burning defect of 0.5mm ², and the latest industry standard requires the exhaust groove depth to be 0.6-0.8 times the material viscosity. A common mistake is excessive opening of exhaust slots leading to sharp edges. The principle of "stepped exhaust" should be followed, with the main parting surface slot depth of 0.03-0.05mm and the auxiliary exhaust plate controlled at 0.015mm.
The timing optimization of the ejection mechanism affects the stability of demolding. The speed of the top rod needs to match the shrinkage rate of the material. For example, POM material needs to be ejected at 10mm/s when cooled to 80 ℃, and a delay of 0.5 seconds will cause a white top defect. The misconception is to ignore the guiding accuracy of the top needle plate, but in reality, it is necessary to ensure that the straightness error of every 100mm stroke is ≤ 0.01mm.
The fine adjustment of gate structure is the key to avoiding flow marks. For high gloss products, the delayed valve gate technology is used to switch to low-speed mode when filling 95%, which can increase the strength of the weld line by 30%. A common mistake is that the gate size is too large, which leads to stress concentration. The design principle of "gate thickness=product wall thickness x 0.6" should be followed.
The efficiency verification of the cooling water circuit determines the production cycle. Although 3D printing of conformal cooling water channels can improve efficiency by 20%, CFD fluid simulation is needed to verify whether the pressure drop exceeds the standard. The misconception is to blindly increase the number of waterways, but in reality, the distance between adjacent waterways should be kept at least 3 times the aperture to avoid thermal interference.
The dynamic compensation of material behavior is the ultimate challenge. By 2025, the intelligent compensation system will be able to automatically adjust the material temperature based on environmental humidity. For example, for every 0.02% increase in ABS moisture content, the melt temperature needs to be reduced by 3 ℃. The biggest misconception is to rely on static shrinkage rate data and ignore dynamic variables in the production process.
The essence of plastic mold debugging is the precise balance of multiple variables. From strict control of mold temperature ± 1 ℃ to exhaust optimization at 0.01mm level, data models need to be established for every detail. Leading enterprises have begun to apply digital twin technology, completing 90% of debugging work in virtual environments, reducing the number of trial molds from 15 to 3. In the future, with the application of quantum sensing technology, plastic mold debugging will enter the era of atomic level precision, driving the manufacturing industry towards the goal of "zero defects".