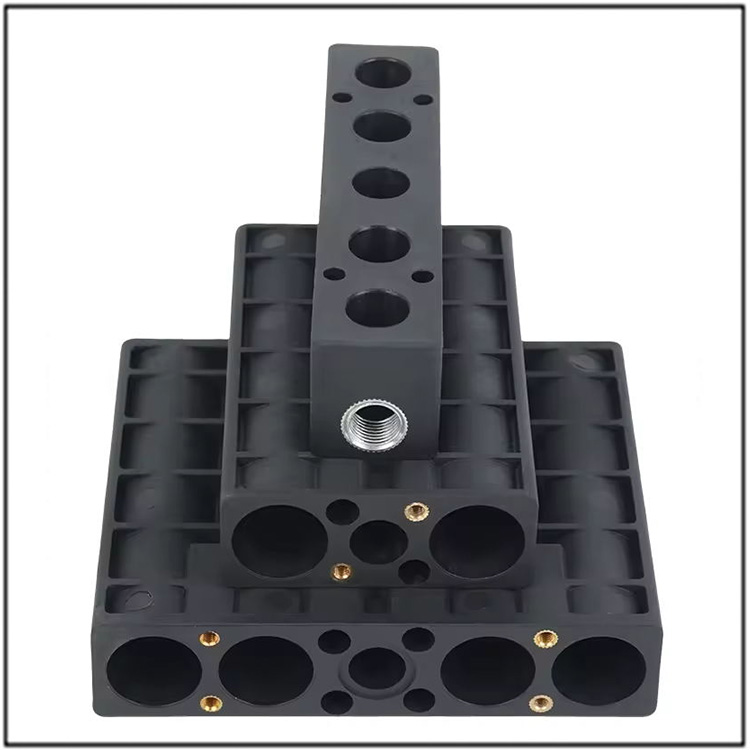
Analysis of The 5 Major Causes of Bubble Problems in Injection Molds
In the precision injection molding production process, bubble defects are always the primary problem that troubles the quality of plastic products. The latest industry report for 2025 shows that about 32% of injection molded defective products are directly related to bubble problems, especially in the fields of medical and optical components, where micrometer sized bubbles may cause product functional failure. This article will delve into the core mechanism of bubble generation in injection molds and provide solutions that have been validated in production.
The material factor is the intrinsic cause of bubble formation. When the moisture content of plastic particles exceeds 0.02%, they will rapidly vaporize in high temperature environments above 200 ℃. Experimental data shows that when 1 gram of PP material contains 0.05% moisture, about 12cm ³ of water vapor will be generated, which is sufficient to form a bubble group with a diameter of 0.3mm inside the product. The volatile substances in modified materials cannot be ignored, especially when adding 30% recycled materials, the amount of gas produced by the decomposition of low molecular weight substances will increase by more than three times.
The design flaw of the mold exhaust system is the key to the accumulation of bubbles. According to the revised mold design specifications in 2025, the depth of the exhaust groove should be controlled at 0.6-0.8 times the viscosity of the material melt. For example, when processing PA66, an exhaust depth of 0.03mm can achieve a gas escape velocity of 15cm/s. However, caution should be taken against the problem of excessive exhaust causing sharp edges. A reasonable approach is to install a main exhaust groove of 0.02-0.04mm on the parting surface and an auxiliary exhaust channel of 0.01-0.015mm in the gap between the top pins.
Improper setting of process parameters can exacerbate the generation of bubbles. When the injection speed exceeds 120mm/s, air will be trapped at the front end of the melt to form vortex air pockets. The latest intelligent injection molding machine adopts segmented injection control, switching to a low-speed mode of 30mm/s after filling 90% of the volume, allowing sufficient time for the cavity gas to be discharged from the exhaust system. Insufficient holding pressure is equally fatal. When the pressure is lower than 80% of the solidification pressure of the melt, gases dissolved in the material will re accumulate, which is particularly evident during the cooling process of thick walled products.
Imbalance in temperature control can trigger the decomposition of bubbles. When the temperature of the material barrel exceeds the recommended upper limit of 15 ℃, engineering plastics such as PA6 will decompose and produce 0.8% of gas per hour. The electromagnetic induction heating system launched in 2025 can control temperature fluctuations within ± 0.5 ℃, reducing material thermal degradation rate by 60% compared to traditional resistance heating methods. The temperature gradient of the mold cannot be ignored. When the local mold temperature differs by more than 20 ℃, vacuum bubbles will form at the melt interface with different cooling rates.
When spraying water-based release agents excessively, a 5 μ m thick film layer will vaporize at high temperatures, forming a dense group of surface bubbles. Experiments have shown that using nanoscale fluorine coating instead of traditional release agents can reduce the spraying amount by 70% while controlling the surface bubble diameter of the product to below 10 μ m. For transparent materials such as PC, it is recommended to use ionization vapor deposition technology to form an ultra-thin release film of 0.1 μ m on the mold surface, which ensures smooth demolding and avoids the generation of bubbles.
To solve the problem of air bubbles in injection molds, a systematic prevention and control system needs to be established. From vacuum drying in the material pretreatment stage, to CFD exhaust simulation in the mold design stage, to multi parameter collaborative control in the production process, every link must be strictly controlled.