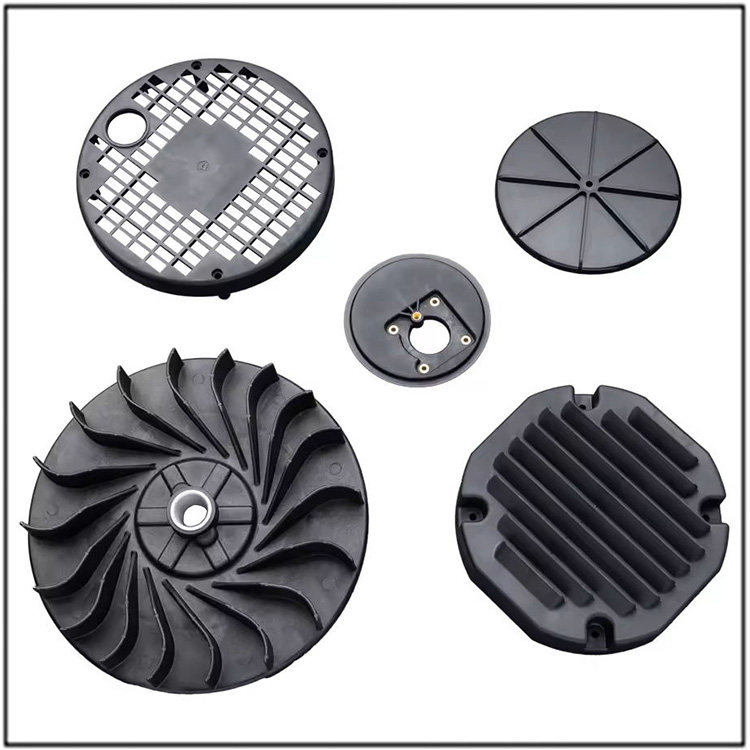
What are The Process Conditions For PVC Plastic Injection Molding?
In the field of plastic processing, PVC (polyvinyl chloride) has attracted much attention for its unique physical properties and wide range of applications. From home decoration to industrial manufacturing, PVC products are everywhere. So, what are the conditions required for the key process of PVC plastic injection molding to ensure excellent product quality? Today, let's uncover them one by one
In the PVC plastic injection molding process, temperature is one of the primary factors to consider. The temperature of the material barrel needs to be accurately set according to the characteristics of PVC material, ensuring that the material is fully melted while avoiding overheating that may cause decomposition. At the same time, the mold temperature also needs to be carefully controlled to ensure uniform cooling of the plastic inside the mold cavity, reducing shrinkage and deformation. The precise control of temperature, like the control of heat in cooking, is the key to achieving high-quality PVC products.
The pressure and speed during the injection molding process are equally important. High pressure can ensure that PVC material fully fills the mold, but excessive pressure may also cause mold damage or increase internal stress in the product. Therefore, it is necessary to find a balance point between pressure and speed, ensuring both injection efficiency and product quality. This process is like carefully carving an artwork, requiring the patience and skill of the craftsman.
Mold design is another core link in the PVC injection molding process. Excellent mold design should fully consider the fluidity and cooling performance of materials, ensuring that plastics can be filled smoothly and cooled evenly. At the same time, the exhaust system of the mold also needs to be carefully arranged to avoid the generation of bubbles and defects.
Pre treatment of PVC material is also an essential step before injection molding. Appropriate drying treatment can remove moisture and volatile substances from materials, improving their plasticizing effect and stability. In addition, it is necessary to screen and mix the materials to ensure their uniformity and consistency. The adequacy of material preparation directly affects the smooth progress of injection molding and the quality of the final product.
In addition to the above process conditions, environmental control in the injection molding workshop cannot be ignored. Stable temperature, humidity, and cleanliness are important factors in ensuring the smooth progress of the injection molding process and stable product quality. A good injection molding environment can reduce the interference of external factors on the production process, improve production efficiency and product quality.