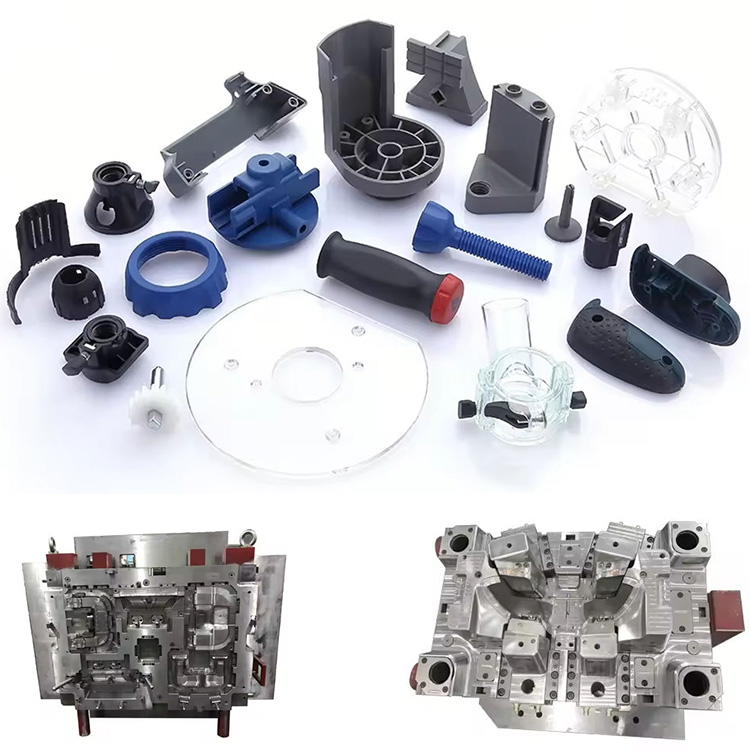
Why Do Plastic Molds Need to Be Done Cold Runner?
Plastic molds undergo severe tests of high temperature and high pressure during the injection molding process. This process not only tests the material and craftsmanship of the mold, but also places extremely high demands on the temperature management of the mold. The cold runner system serves as the "temperature regulator" inside the mold, effectively removing heat from the surface of the mold through the circulating water medium, preventing damage to the mold due to overheating. This precise temperature control mechanism not only extends the service life of the mold, but also lays a solid foundation for efficient and stable subsequent production.
Plastic molds require the cold runner for the following reasons:
1,Improve the service life of molds
·During the plastic molding process, the mold is affected by various factors such as high temperature, high pressure, and chemical corrosion, which can easily lead to problems such as corrosion, wear, and cracking of the mold. By using a water transportation system, the mold can be effectively cooled, the mold temperature can be reduced, thereby slowing down the damage of these adverse factors to the mold and extending its service life.
2,Improve the quality of plastic parts
·The temperature of plastic molds has a significant impact on the shape, size, surface smoothness, and dimensional accuracy of products. By controlling the temperature of the mold, the water transportation system can avoid quality problems such as deformation, shrinkage, and bubbles caused by excessively high or low temperatures, thereby improving the overall quality of the plastic parts.
3,Improve production efficiency
·During the plastic molding process, it is required that the mold has a fast cooling rate to improve production efficiency. The water transportation system uses water as a heat dissipation medium to achieve rapid cooling of the mold through circulating flow, thereby shortening the production cycle and improving production efficiency.
4,Reduce production costs
·Appropriate cooling can reduce the cost of frequent maintenance or replacement of molds due to overheating. Meanwhile, improving production efficiency and plastic part quality can also help reduce scrap rates and production costs.
5,Specific design principles
When designing the cold runner system for plastic molds, a series of principles need to be followed, such as placing the cold runner as close to the surface of the mold cavity (core) as possible, ensuring uniform and tightly arranged water transport diameters, and adopting a multi loop design to improve cooling efficiency. These principles aim to ensure that the cold runner system can effectively cool the mold while avoiding unnecessary damage to the mold.
6,Resolve common issues
In the actual production process, there may be issues such as blockages in the cold runner system. For general blockages, tools such as air guns can be used to clear them; For severe blockages, it is necessary to remove the mold and disassemble and clean the waterway. In addition, it is necessary to regularly clean the circulating water pipeline and apply appropriate cleaning agents, softeners, and anti algae agents to maintain the cleanliness and stability of the water quality.