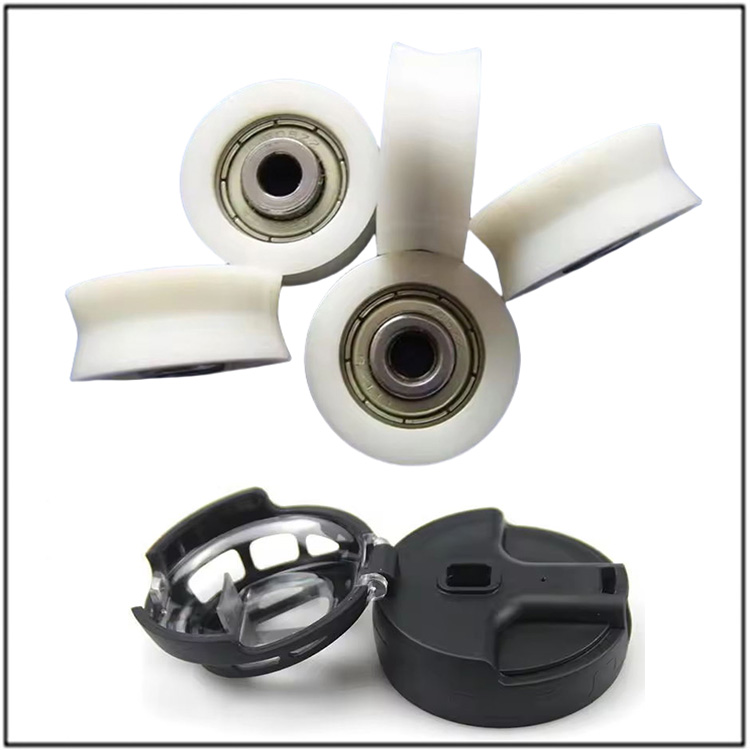
What are The Main Standards For Injection Molded Electronic Casings?
In the electronic manufacturing industry, injection molding is one of the main processes for producing electronic casings. Electronic casings not only need to protect internal components, but also meet various requirements such as appearance, size, and functionality. Therefore, when designing injection molded electronic casings, a series of standards must be followed to ensure the high quality and reliability of the product.
Firstly, dimensional accuracy is one of the core requirements for electronic casing design. The size of the electronic casing directly affects its assembly effect with internal components, so in the injection molding process, the dimensional tolerance must be strictly controlled, usually within ± 0.1mm. At the same time, the accuracy of the mold is also crucial. High precision molds can ensure the stability of the formed dimensions and avoid assembly problems.
Secondly, the appearance quality is the user's first impression of the electronic casing. The surface of the shell should be smooth and flawless, usually requiring a mirror effect. In addition, mold design should avoid flying edges and burrs, ensure smooth edges, and enhance the overall grade of the product. The appearance quality not only affects aesthetics, but also relates to the user's experience.
Material selection is another key factor in the design of electronic casings. Common materials include ABS plastic, PC plastic, and flame-retardant materials. ABS plastic has high strength and impact resistance, suitable for general electronic casings; PC plastic has high transparency and high temperature resistance, suitable for high-end electronic products; Flame retardant materials such as flame-retardant ABS or PC can meet safety certification requirements and ensure the safety of the product during use.
In terms of structural design, electronic casings need to balance protection and functionality. The wall thickness is usually designed to be 2-3mm to avoid deformation or insufficient strength caused by being too thick or too thin. The reasonable arrangement of reinforcing ribs can improve the rigidity of the shell, while the design of heat dissipation holes needs to be optimized according to the heat dissipation requirements of electronic components to ensure the stability of the product during long-term use.
In addition, electronic casings also need to undergo a series of environmental tests to ensure their reliability in practical use. The temperature resistance test requires the shell to not deform or crack in high and low temperature environments; The weather resistance test requires the shell to be able to resist the influence of environmental factors such as ultraviolet rays and moisture; Flame retardant testing requires certification such as UL94 to ensure the safety of the product.
Finally, production efficiency is also an important factor to consider when injection molding electronic casings. The use of multi cavity molds or hot runner systems can significantly improve production efficiency, while optimizing molding parameters such as injection pressure, temperature, and time to ensure the stability of the molding process and reduce waste rates.
In summary, the design and manufacturing of injection molded electronic casings require comprehensive consideration of various standards such as dimensional accuracy, appearance quality, material selection, structural design, environmental adaptability, and production efficiency. Through reasonable design and strict process control, you can create high-quality electronic casings.