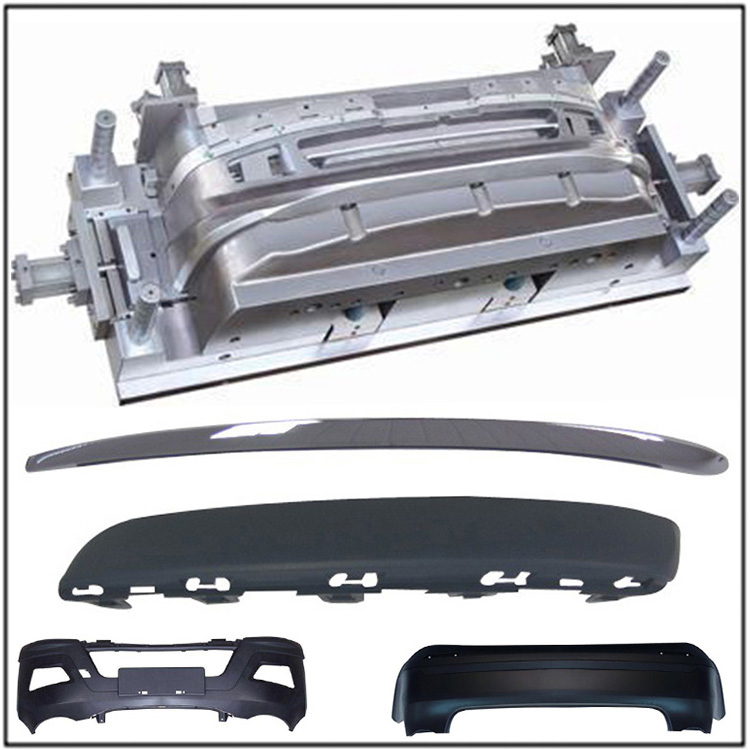
How to Match the Inlet of The Plastic Mold Temperature Controller?
In the production process of plastic molds, the precise matching between the temperature control system and the inlet directly affects the quality of product molding. Due to the use of multi nozzle structures in modern molds, operators often face a technical challenge: how to quickly confirm the actual heating area controlled by a temperature controller? This is not only related to the stability of the injection molding process, but also closely related to core indicators such as product dimensional accuracy and surface smoothness. This article will start from practical application scenarios and systematically analyze three effective methods that have been verified by the industry.
When the plastic mold is equipped with complete technical documentation, the most direct way is to verify the wiring topology diagram provided by the hot runner system supplier. Professional manufacturers usually install stainless steel identification plates inside the junction box or on the side wall of the mold, using a combination of letters and numbers to label the corresponding hot nozzle number for each temperature control channel. For example, the interface labeled as "TC03-Z12" indicates that the temperature controller controls the heating function of the 12th hot nozzle in the Z area of the mold. This type of information often forms a complete technical file with the mold assembly drawing and electrical schematic diagram, and operators can quickly lock the corresponding relationship through cross validation. It should be noted that some imported molds may use internationally recognized color code systems, such as red sleeves corresponding to temperature zone 1, yellow corresponding to temperature zone 2, etc. At this time, it is necessary to identify them in conjunction with the color code comparison table in the equipment manual.
For old molds lacking a labeling system, a step-by-step heating verification method can be used. When performing specific operations, first set the other temperature control channels to room temperature mode, activate the target temperature controller separately, and increase the temperature setting value to 20-30 ℃ higher than the normal operating temperature. During the heating process of the mold, an infrared thermal imaging device is used to scan key parts such as the splitter plate and hot nozzle in real time. The area where the temperature rises the fastest and eventually reaches the set value is the control range of the temperature controller. A certain automobile parts manufacturing enterprise once successfully located the corresponding hot nozzle of the abnormal temperature controller in the 48 cavity mold within 15 minutes through this method, avoiding the disassembly and repair of the entire mold. It should be emphasized that safety measures must be taken during the implementation of this method, especially when dealing with molds made of high-temperature materials such as PPS and LCP. Temperature measurement operations must maintain a safe distance of at least 1 meter.
Establishing digital temperature records is a long-term solution for dealing with complex mold systems. By recording the temperature rise curves, steady-state deviations, and other data of each channel during each temperature control cycle, and combining them with the position of the hot nozzle, a three-dimensional temperature distribution model is established. A precision connector manufacturer imported MES system to digitize and bind information such as mold number, temperature controller serial number, and corresponding hot nozzle coordinates, allowing operators to scan codes to retrieve historical data. When temperature anomalies occur, the system can automatically compare the current data with historical benchmark values, with an accuracy rate of over 98%. This intelligent management method not only solves the problem of identifying corresponding relationships, but also provides data support for preventive maintenance.
The temperature control of plastic molds is essentially the precise regulation of material flowability. Operators should flexibly choose identification strategies based on factors such as mold structure complexity and production batch size in practice. For standardized mass production molds, priority should be given to using the technical document verification method; The step-by-step heating method is more effective in dealing with emergency malfunctions or mold modifications; Long term precision molds are suitable for establishing a full lifecycle temperature database. Mastering the core logic of these methods is essential to ensure that each temperature control signal accurately reaches the target inlet, laying the foundation for producing high-quality plastic products.