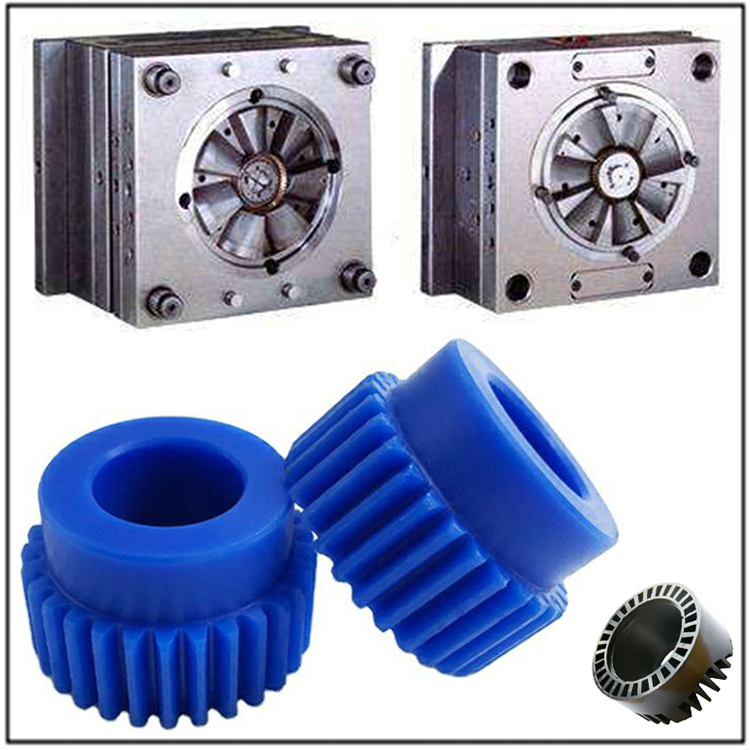
How to Distinguish The Tritan and PPSU Materials in Injection Molding?
In the field of injection molding, Tritan and PPSU, as two types of high-performance engineering plastics, are widely used in different industries due to their unique performance advantages. However, many practitioners still face confusion when selecting materials in practice: what are the differences between these two materials in terms of essential characteristics, processing parameters, and end applications? This article will conduct in-depth analysis from three dimensions: molecular structure, processing adaptability, and scene adaptability
From the perspective of molecular composition, Tritan (chemical name: modified copolyester) was developed by Eastman Company. Its molecular chain forms a flexible structure through the copolymerization reaction of cyclohexanedimethanol and terephthalic acid. This design combines high transparency and impact resistance, with a transmittance of over 92% and a notch impact strength of up to 850J/m. The main chain of PPSU (polyphenylene sulfone resin) is embedded with a rigid structure of sulfone groups and aromatic rings, which endows it with excellent high temperature resistance. It can withstand temperatures up to 180 ℃ for a long time and has an instantaneous peak heat resistance exceeding 220 ℃. A comparative experiment conducted by a third-party testing institution showed that under a steam sterilization environment at 121 ℃, the dimensional stability of PPSU products increased by 40% compared to Tritan, confirming the essential difference in thermal stability between the two. The differentiation of application scenarios arises from the differential expression of material properties. Tritan holds a dominant position in the field of infant and children's products with its FDA food grade certification and EU 10/2011 standards. Its outstanding resistance to chemical corrosion and ability to withstand extreme environments with pH values ranging from 1 to 14. A portable baby bottle made by Tritan was used by an international mother and baby brand, which maintained over 95% light transmittance and drop resistance during accelerated aging tests simulating a 3-year usage cycle. PPSU, relying on USP Class VI biocompatibility certification, has become the preferred material for medical sterilization equipment. The surgical instrument tray of a tertiary hospital is injection molded with PPSU, and after 500 rounds of gamma ray sterilization, the mechanical performance degradation rate is less than 3%, significantly better than traditional metal materials.
In the injection molding process, there is a significant difference in the process adaptability between the two. The melting temperature range of Tritan is concentrated between 245-275 ℃. Due to its high melt flow rate of 25g/10min (testing conditions of 280 ℃/2.16kg), a stepped injection molding process can be used to reduce internal stress. It is recommended to control the mold temperature between 55-75 ℃ to balance crystallinity and molding efficiency. The processing temperature of PPSU needs to be increased to 310-340 ℃. Due to the melt viscosity being three times higher than Tritan, dynamic pressure holding technology is often required to ensure the filling integrity of complex structures. The difference in secondary processing performance directly affects production costs and efficiency. Tritan can achieve seamless bonding through conventional UV curing adhesive, with a surface energy of up to 38mN/m and a 50% increase in adhesion to electroplated layers compared to PC materials. It is suitable for vacuum coating processes in high-end cosmetic packaging. The laser welding performance of PPSU is more outstanding. In medical device assembly, the use of a 1064nm wavelength laser can achieve precise packaging of 0.2mm welds, and the pass rate of airtightness testing is as high as 99.8%.
From the perspective of full lifecycle cost analysis, Tritan's raw material price is about 65% of PPSU, but its durability in high temperature and high humidity environments is relatively limited, making it suitable for iterative products in the fast-moving consumer goods field. Although the initial cost of PPSU is relatively high, in the repeated sterilization use scenario in the medical field, the single use cost can be reduced to 1/5 of that of metal instruments. With the development of material modification technology, Tritan can increase its surface hardness to 3H pencil level by adding nano silicon oxide, while the composite modification of PPSU and carbon fiber can break through 9GPa in bending modulus. These evolutionary directions are continuously expanding the application boundaries of both.