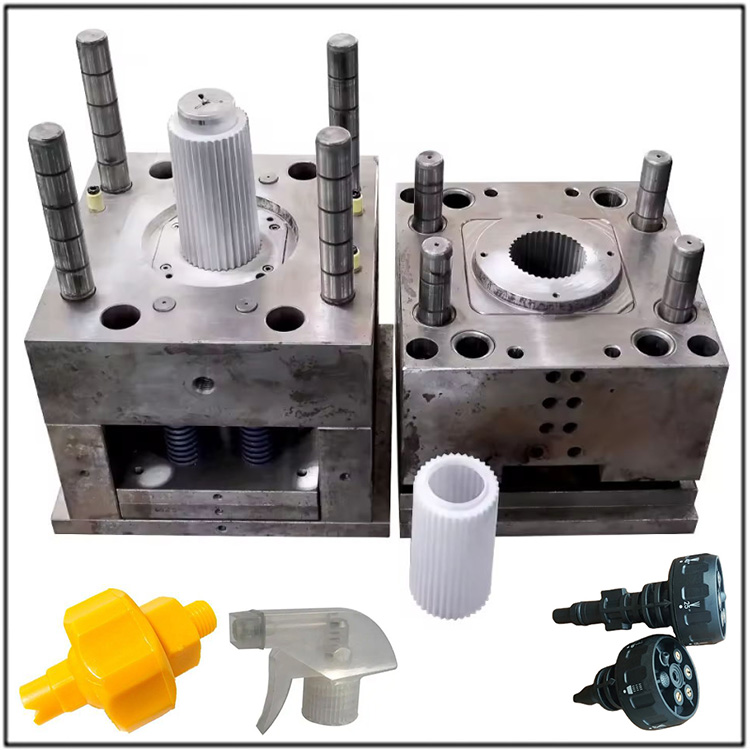
Is The Plastic Bottle Mouth By Injection Molded or Blow Molded?
Plastic bottles, as the core carrier of modern packaging, often determine the functionality and quality of the product through the details of their production process. Consumers may rarely think about why the thread on the bottle mouth can perfectly match the bottle cap, while the bottle body can be lightweight and sturdy? The answer lies in the synergistic combination of injection molding and blow molding processes.
From a technological perspective, the manufacturing of plastic bottles is not the result of a single process. Taking common beverage bottles as an example, the bottle mouth is usually completed by injection molding. The injection molding process involves high-pressure injection of molten plastic into precision molds, allowing for precise control of key structures such as the threads and sealing surfaces of the bottle mouth, with errors controlled at the micrometer level. This high-precision feature ensures the sealing of bottle caps during repeated opening and closing, especially suitable for fields such as food and medicine that require strict hygiene. The formation of the bottle body relies on blow molding: the prefabricated tubular billet is heated and placed in a mold, and then blown into shape by compressed air. The advantage of blow molding technology lies in the rapid shaping of hollow structures and its low cost, making it suitable for large-scale production.
It is worth noting that the high-end packaging field often adopts the injection blowing integrated process. For example, in medical eye drops bottles, the bottle mouth is designed to ensure precise dripping of the medication through injection molding, while the bottle body is lightweight and transparent through blow molding. This combination process not only retains the attention to detail in injection molding, but also leverages the economy of blow molding, making it particularly suitable for small capacity, high value-added products.
The selection of materials also affects the process path. PET material is widely used in mineral water bottles due to its high transparency and strong chemical resistance. Its production often adopts injection molding and blow molding: the bottle mouth and preform are first injected, and then the compressive strength of the bottle body is improved through bi-directional stretch blow molding. However, HDPE detergent bottles may be directly molded using blow molding technology in one step to reduce production costs due to lower requirements for bottle mouth accuracy.