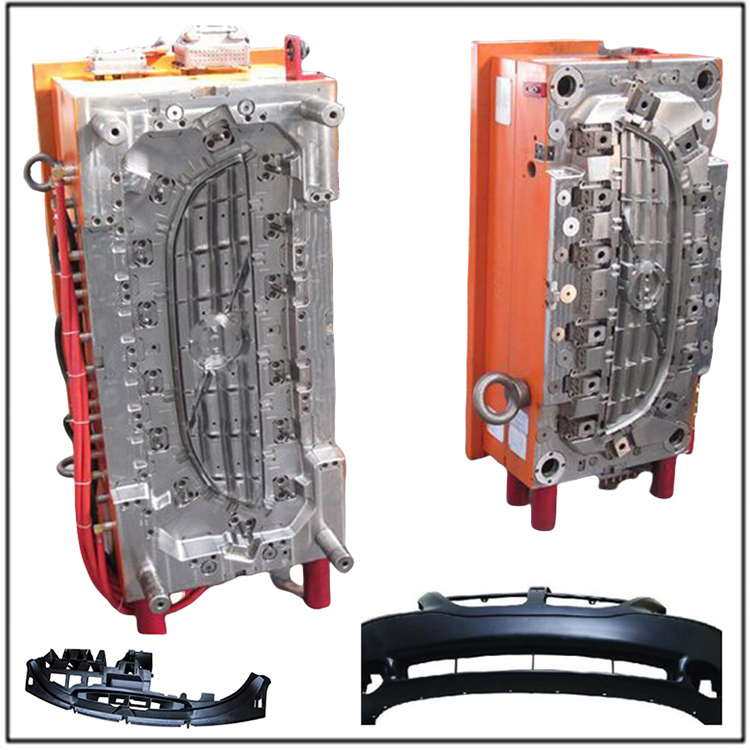
How to Select Plastic Mold Materials and Hardness?
In the field of plastic mold manufacturing, the choice of materials and hardness directly affects the mold life, production cost, and product accuracy. This decision requires a comprehensive consideration of the dynamic balance between material properties, processing technology, and product requirements, rather than a simple empirical value.
The starting point for material selection lies in the analysis of product characteristics. For corrosive plastics such as fiberglass reinforced nylon, corrosion-resistant S136 stainless steel should be selected, with a hardness usually controlled between 48-52HRC and a surface polished to Ra0.02 μ m to resist fiberglass erosion. The mold for producing ordinary PP products can meet the demand by using pre hardened steel P20 (hardness 28-32HRC), which reduces the cost by 40% compared to tool steel. A certain car lampshade manufacturer increased the mold life from 150000 mold cycles to 500000 mold cycles by changing the material from H13 to corrosion-resistant steel.
The weight of production batches is often underestimated. Small batch trial production (<10000 pieces) can use aluminum alloy materials, which have a thermal conductivity five times that of steel and a 30% reduction in cooling time. Although the hardness is only 80-100HB, the advantage of rapid iteration is significant. On the contrary, for million level production molds, DC53 steel (hardness 58-62HRC) that has undergone quenching treatment should be selected. Although the initial cost increases by 50%, the single piece cost decreases by 35%.
The design of the cooling system requires reverse constraint on material selection. When using 3D printed conformal waterway, a copper alloy substrate with a thermal conductivity coefficient of ≥ 40W/m · K needs to be selected. Although its hardness is only 25-30HRC, the cooling efficiency is improved by 60%, effectively compensating for the defect of insufficient hardness. A certain medical catheter mold has shortened the molding cycle from 25 seconds to 18 seconds through this solution, while maintaining a dimensional accuracy of ± 0.02mm.
Surface treatment technology expands the boundaries of material properties. After nitriding treatment, the surface hardness of ordinary 45 steel can reach 1000HV, and the wear resistance is increased by 5 times, while the core maintains a toughness of 30HRC. A certain electronic connector manufacturer adopts this process to reduce mold costs by 25% while ensuring the strength of the top pin system. PVD coating technology can further reduce the friction coefficient to below 0.1, making it particularly suitable for demolding transparent parts.
Under the trend of intelligence, data-driven selection has become a new direction. By establishing a material database and inputting parameters such as product structure, plastic type, and expected output, AI algorithms can recommend the optimal solution.
The cost model needs to be included in the full lifecycle assessment. The procurement cost of high hardness mold steel is 2-3 times higher than that of ordinary steel, but after including maintenance, mold replacement, and scrap losses, the total cost is actually lower in orders of more than 100000 pieces.
The key to achieving scientific selection lies in building a multidimensional decision-making system: establishing a correlation model between material properties and processing costs, quantifying the functional relationship between hardness and wear resistance, and transforming product accuracy requirements into mold rigidity indicators. Professional mold suppliers are usually equipped with material laboratories and simulation analysis software, which can provide customers with a full process service from metallographic analysis to mold flow simulation.
Under the background of industrial upgrading, new composite materials continue to emerge. The specific strength of carbon fiber reinforced mold steel is three times that of traditional materials, and its hardness can reach 55HRC, providing a new choice for ultra precision mold manufacturing. Choosing solutions that keep up with the times will become the key for enterprises to break through in fierce competition.