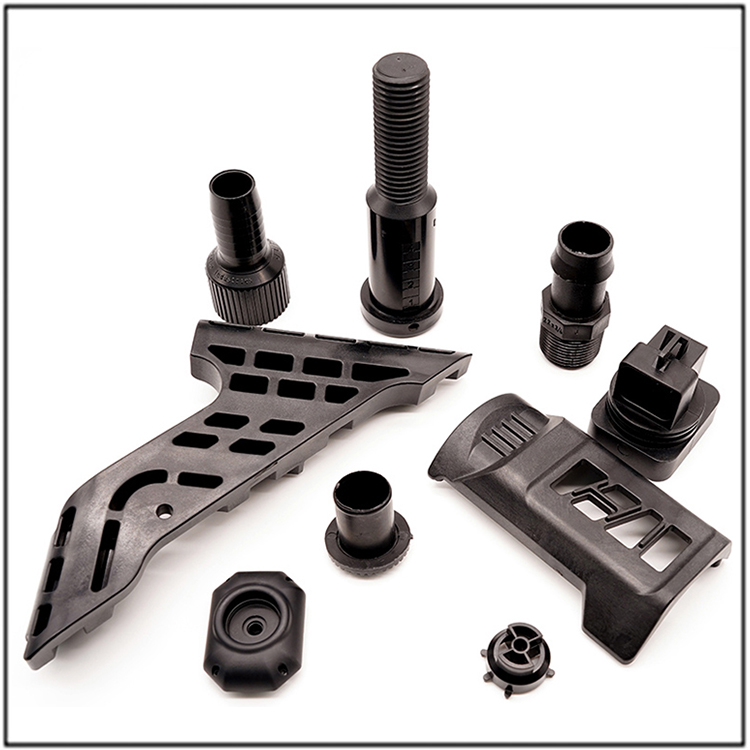
Why Do PP Injection Molded Products Shrinkage Deformation?
In the injection molding process, polypropylene (PP) material is widely used due to its excellent chemical resistance, lightweight, and low cost, but shrinkage has always been a common problem that troubles production quality. Shrinkage not only affects the dimensional accuracy of the product, but may also lead to defects such as surface indentation, warping, and deformation, ultimately affecting assembly performance and service life. So, what factors are causing the shrinkage of PP injection molded products?
Firstly, the crystallization characteristics of the material itself are one of the fundamental reasons for shrinkage. PP belongs to semi crystalline plastics, and during the cooling process, the molecular chains will rearrange from the molten state into an ordered crystal structure, accompanied by volume shrinkage. The higher the crystallinity, the greater the shrinkage rate. Generally, the shrinkage rate of PP is between 1.5% and 2.5%, which is much higher than that of amorphous plastics such as ABS and PC. In addition, different grades of PP materials have different shrinkage rates due to factors such as molecular weight distribution and copolymerization modification. For example, high fluidity PP has shorter molecular chains, faster crystallization speed, and often higher shrinkage rate than low fluidity PP.
Secondly, the setting of injection molding process parameters directly affects the degree of shrinkage. Excessive melt temperature can lead to material degradation, molecular chain breakage, and uneven shrinkage during cooling; However, if the temperature is too low, it may cause insufficient filling and exacerbate local shrinkage. The pressure and time during the holding pressure stage are particularly critical. If the holding pressure is insufficient, the melt cannot be fully replenished during the cooling process, and vacuum bubbles will form inside the product, resulting in surface depressions. According to test data from a certain automotive parts manufacturer, increasing the holding pressure by 15% can reduce the shrinkage rate of PP bumpers from 2.1% to 1.7%, significantly improving dimensional stability. In addition, insufficient cooling time can cause residual heat to remain inside the product during demolding, leading to further shrinkage and deformation.
Mold design also has a significant impact on shrinkage. The position of the sprue determines the flow path of the melt. If the sprue size is too small or unevenly distributed, it will cause local pressure loss, resulting in inconsistent shrinkage rates in different areas. For example, thin-walled areas cool faster and shrink less, while thick walled areas cool slower and shrink more noticeably. This difference can lead to warping deformation. A reasonable layout of cooling water channels can ensure uniform heat dissipation and reduce stress concentration caused by temperature differences. After optimizing the mold cooling system of a certain household appliance enterprise, the warpage deformation of the PP shell was reduced by 40%. In addition, insufficient demolding slope can cause additional stretching of the product during ejection, exacerbating shrinkage deformation.
Environmental factors cannot be ignored either. Although PP has low moisture absorption, if the raw materials are stored improperly, trace amounts of moisture can vaporize at high temperatures, forming bubbles that affect the uniformity of shrinkage. The temperature and humidity changes in the environment after molding may lead to post shrinkage, especially in seasons with large temperature differences, and the size of the product may still change after being placed for several days. A precision parts manufacturer has found that PP gears produced in winter will shrink in inner diameter by 0.05mm after being left at room temperature for 72 hours. Therefore, post-treatment must be carried out in a constant temperature and humidity environment. To effectively control the shrinkage of PP injection molded products, systematic measures need to be taken. In terms of material selection, low shrinkage modified PP or the addition of nucleating agents can be chosen to reduce crystallinity; Optimize the pressure holding curve and cooling time in the process to ensure sufficient shrinkage compensation; Mold design should follow the principle of balanced flow and adopt conformal cooling technology to improve heat dissipation efficiency. In addition, annealing treatment can release residual stress and further stabilize the size. Only by comprehensively considering materials, processes, molds, and environmental factors can shrinkage defects be minimized to the greatest extent and the market competitiveness of PP injection molded products be enhanced.