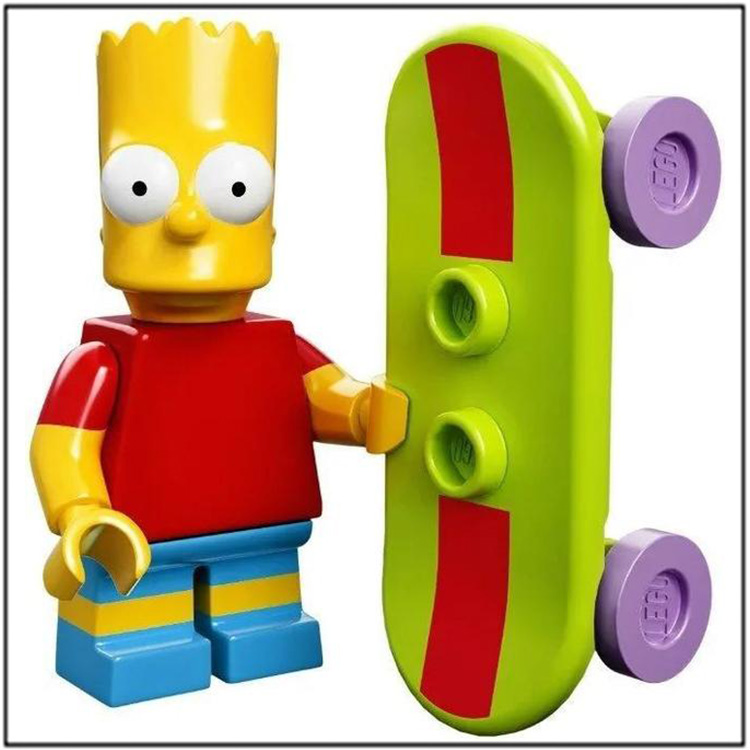
0.4 Smoothness of Plastic Molds
In the field of precision injection molding, the smoothness of the mold surface directly affects the appearance quality and demolding performance of the product. When the industry standard mentions "0.4 smoothness of plastic molds", what level of craftsmanship does this value represent?
The smoothness of 0.4 μ m (Ra value) belongs to the surface treatment category of precision molds, which is equivalent to the second highest level of mirror polishing. From a microscopic perspective, this standard requires that the peak to valley height difference on the surface of the mold cavity be controlled within 0.4 micrometers, which is equivalent to 1/150 of the diameter of a human hair. The mold that achieves this precision can present a glass like texture on the surface of the molded product, while significantly reducing demolding resistance. The test data released by the International Mold Association (IMA) in 2024 shows that when the smoothness is increased from 0.8 μ m to 0.4 μ m, the demolding force of PP material can be reduced by 28%, and the mold life can be extended by more than 30%.
The core technology for achieving a 0.4 smoothness lies in multi-stage precision machining. Firstly, the cavity needs to be roughly machined to Ra 1.6 μ m through CNC milling, followed by semi precision machining (Ra 0.8 μ m) using diamond cutting tools, and finally achieving nanoscale finishing through diamond grinding paste combined with fiber polishing wheels. The practice of a certain automotive lighting mold manufacturer has shown that in a dust-free workshop with a constant temperature of 20 ℃± 1 ℃, using diamond micro powder with a particle size of 3 μ m for 48 hours of continuous polishing can control the directional deviation of surface texture within 5 ° and ensure uniform refraction of light. It is worth noting that the emerging ion beam polishing technology in 2025 can increase processing efficiency by 40% by bombarding the surface atomic layer with argon ions, while avoiding the micro crack problem of traditional mechanical polishing.
The material properties play a decisive role in maintaining smoothness. NAK80 pre hardened steel has become the preferred material for 0.4 degree smooth molds due to its uniform distribution of carbides. Its Vickers hardness reaches HRC 40-42, and the surface roughness only increases by 0.02 μ m after 100000 injection molding cycles. Although S136 corrosion-resistant steel has higher hardness, the carbide particle size is larger, and when polished to 0.4 μ m, it is prone to produce an "orange peel" phenomenon.
The correlation between smoothness and product functionality is particularly prominent in the high-end field. Taking optical lens molds as an example, a surface accuracy of 0.4 μ m can increase the transmittance to 99.2% and haze to below 0.3%. A certain drone camera manufacturer reduced the lens imaging distortion rate from 0.15% to 0.08% by improving the smoothness of the mold. In terms of microstructure injection molding, a substrate smoothness of 0.4 μ m is a prerequisite for achieving nanoimprint texture replication. A certain mobile phone manufacturer used this technology to produce a leather like texture back cover, which achieved industry-leading tactile simulation. With the tightening of environmental regulations, the optimization value of smoothness in molding processes is increasingly prominent. High gloss molds can reduce the locking pressure by 15% -20%, and reduce energy consumption by about 12% when forming biodegradable material PLA. The production data of a certain daily chemical packaging enterprise shows that after improving the mold smoothness from 0.8 μ m to 0.4 μ m, the uniformity of crystallinity distribution of PET preforms increased by 18%, and the qualification rate of bottle mouth sealing increased from 97.3% to 99.6%. It is worth noting that the popularization of digital polishing monitoring systems has brought smoothness control into the intelligent stage. By using laser interferometers to provide real-time feedback on surface morphology, polishing accuracy fluctuations can be controlled within ± 0.02 μ m.
The 0.4 smoothness of plastic molds is not only a technical indicator, but also a microcosm of precision upgrading in the manufacturing industry. From material selection to process innovation, from energy consumption optimization to functional expansion, this value embodies the pursuit of ultimate quality in modern industry.