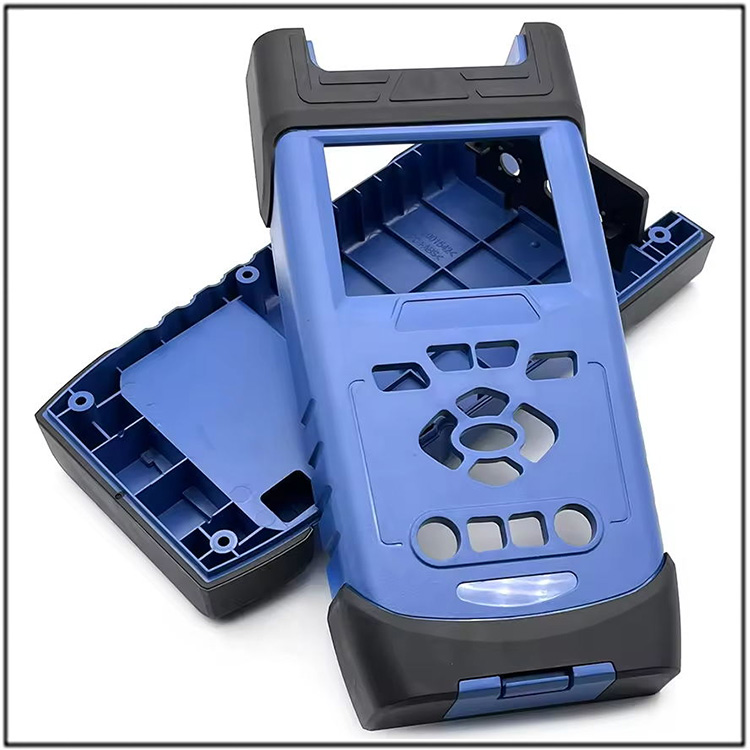
Reason Analysis and Solution For Poor Bonding of TPE Overmolding
In the field of plastic product processing, TPE (thermoplastic elastomer) overmolding technology is widely popular due to its ability to give products a soft touch and multifunctionality. However, poor bonding often troubles the production process, and the main reasons involve the following key factors:
Firstly, there is the issue of material compatibility. The molecular structure differences between TPE and substrates (such as ABS, PC, or PP) directly affect the bonding effect. Taking PP substrate as an example, its non-polar characteristics make it difficult to bond with most TPEs. In this case, a specially modified TPE formula must be selected. According to test data from a certain automotive interior manufacturer, TPE modified with maleic anhydride grafting can increase the peel strength of PP substrate by more than three times.
Process parameter control is equally crucial. During the molding process, the mold temperature needs to be precisely maintained within an appropriate range (usually 30-50 ℃ for TPE and 60-80 ℃ for substrate). Low temperature can lead to poor material flowability, while high temperature may cause TPE degradation. It is recommended to control the injection pressure within the range of 60-100MPa, with a holding time of no less than 5 seconds, to ensure that the material is fully bonded. A production case of a medical controller shows that after increasing the nozzle temperature by 5 ℃, the product yield rate jumped from 82% to 95%.
Surface treatment of substrates is often overlooked but extremely critical. The oxide layer or residual release agent on the surface of the substrate will form a barrier layer. Plasma treatment technology can effectively improve surface energy. Experiments have shown that after 30 seconds of 40W plasma treatment, the bonding strength between ABS surface and TPE can be increased by 200%. For products with high production volume, it is recommended to use an online cleaning device to ensure the cleanliness of the substrate surface
Defects in mold design are also common causes. The thickness design of the encapsulation area should not be less than 0.8mm, and the transition area should adopt a sloping or groove structure to increase mechanical interlocking. A certain electric tool manufacturer increased the thickness of the adhesive area from 0.5mm to 1.2mm and changed the edge to a 0.5mm deep serrated structure, which extended the product's service life by three times.
Environmental factors cannot be ignored either. When the humidity exceeds 60%, the material is prone to moisture absorption, leading to the formation of bubbles at the bonding interface. It is recommended to dry TPE for 4 hours/80 ℃ before molding, and maintain a relative humidity of 40% -50% in the workshop. After a certain audio button manufacturer installed a dehumidification system, the seasonal defect rate decreased from 15% to 3%.
To address these issues, the following improvement measures can be taken: establishing a material compatibility database and conducting DSC testing on new material combinations; Real time monitoring of mold temperature using infrared thermometer; Introduce plasma surface treatment equipment; Optimize mold gate design to improve weld line strength. Through systematic process control, the bonding reliability of TPE overmoulding can be significantly improved, creating greater added value for the product.