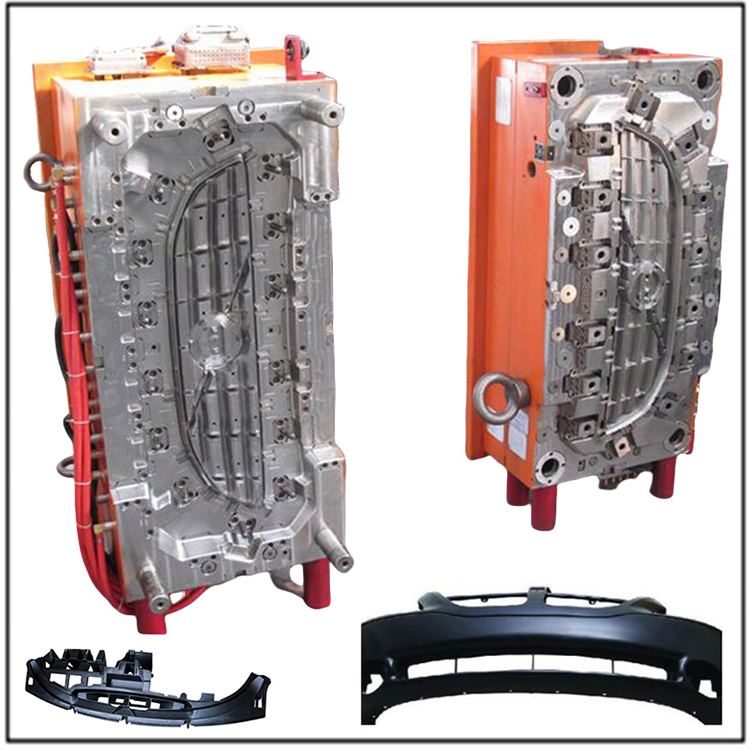
Analysis of Key Technologies for PPSU Injection Molding Matte Products
In the fields of medical equipment and high-end consumer goods manufacturing, PPSU injection molding faces special surface treatment requirements. Although traditional sandblasting technology can achieve matte effect, it has problems such as insufficient durability and high cost. How to directly obtain high-quality matte surface through injection molding process? This requires systematic optimization from three dimensions: material formulation, mold technology, and process control.
The adjustment of material formula is the basis for obtaining matte effect. By adding special matting agents to PPSU raw materials, the surface glossiness (glossiness unit GU value) can be effectively reduced. Experimental data shows that adding 6% nanoscale silica can reduce the surface glossiness of PPSU from 90GU to around 35GU, while maintaining over 90% of the original mechanical properties of the material. This modification method is particularly suitable for medical devices that require frequent disinfection, such as surgical instrument handles and endoscope components.
The surface treatment process of the mold directly affects the final texture of the product. The current mainstream processing methods include:
1.Electrical Discharge Machining (EDM): can form a uniform texture of Ra1.6-3.2 μ m
2.Laser etching technology: capable of producing precise micro pore structures of 0.5-2 μ m
A case study of a mold company shows that molds using laser etching technology can maintain a stable matte effect even after 50000 production cycles, far exceeding the 20000 service life of traditional sandblasting molds.
The control of injection molding process is particularly crucial. Suggest using the following parameter combinations:
-Melt temperature: 330-350 ℃ (± 3 ℃)
-Injection pressure: Adjust according to texture depth, usually requiring an increase of 15-20%
-Segmented injection: Fill the cavity body at medium speed first, and then complete texture replication at low speed
A company has reduced the defect rate of PPSU matte parts from 15% to below 3% by optimizing process parameters.
The design of cooling systems is often overlooked, but it is crucial. Controlling the mold temperature within the range of 120-140 ℃, combined with a conformal cooling water circuit design, can result in better surface quality of the product. Practical application has shown that this design can improve the scratch resistance of matte surfaces by more than 40%.
In terms of quality inspection, it is recommended to adopt:
-60 ° Glossmeter: Monitor surface glossiness fluctuations
-Electron microscope: Observing the completeness of texture replication
-Automated visual inspection: achieving 100% full inspection
With technological advancements, the application areas of PPSU matte injection molded products are constantly expanding. In the medical industry, it is used to manufacture matte instrument handles that are resistant to high temperature disinfection; In the field of consumer electronics, matte shells are used to produce high-end headphones; In the automotive industry, it is used to create matte interior parts with excellent weather resistance.