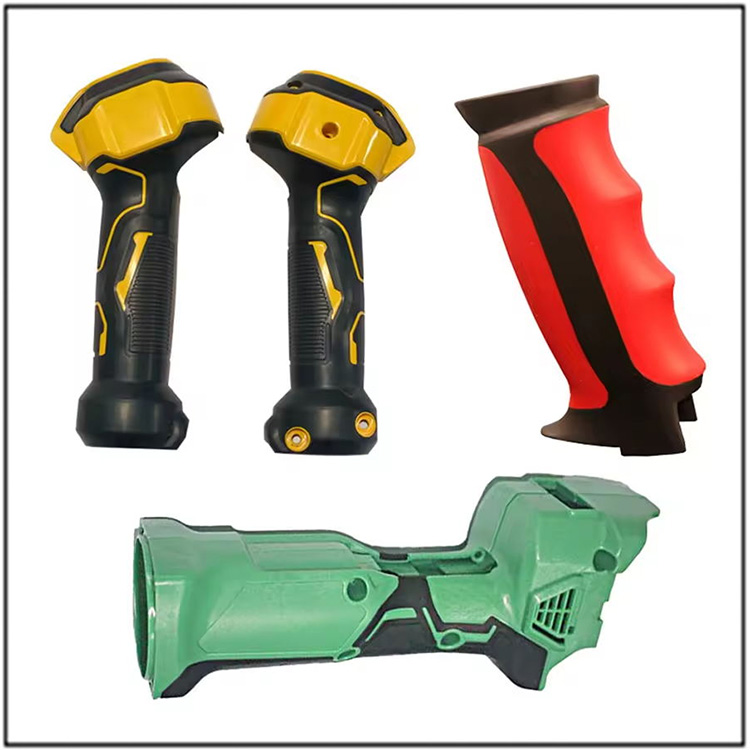
Why is The Hardness of The Front Mold Higher Than The Mold Core For The Plastic Molds?
In the field of plastic mold manufacturing, the design of the hardness difference between the front mold (fixed mold) and the mold core (moving mold) contains precise thermodynamic and mechanical principles. This differentiated hardness strategy is not accidental, but based on a comprehensive consideration of the force characteristics, wear laws, and cost control throughout the entire life cycle of the mold, which directly affects product accuracy and production efficiency.
From the perspective of functional division of labor, the front mold, as the first contact surface for filling the melt, needs to withstand instantaneous pressures of up to 150MPa and melt temperatures above 300 ℃ during the injection stage. Taking the car lampshade mold as an example, the front mold surface will experience more than 10 ^ 5 thermal cycles of impact during continuous production, and ordinary P20 steel is prone to thermal fatigue cracks under this condition. Therefore, the front mold usually uses pre hardened steel (such as H13) and increases its hardness to 48-52HRC through vacuum heat treatment, forming a significant gradient compared to the 38-42HRC of the rear mold. Experimental data shows that increasing hardness by 5HRC can extend the wear resistance life of the front mold by more than three times.
Thermal deformation control is another key factor. During the injection molding process, the temperature fluctuation of the front mold can reach 80-120 ℃, and the coefficient of thermal expansion is negatively correlated with the material hardness. When the temperature of the plastic mold rises from 25 ℃ to 150 ℃, the change in cavity size of the low hardness front mold is 2.3 times that of the high hardness mold. The actual test results of a certain connector mold show that after increasing the hardness of the front mold from 40HRC to 50HRC, the product size fluctuation range is reduced from ± 0.15mm to ± 0.05mm, meeting the requirements of precision injection molding.
From an economic perspective, differentiated hardness design can optimize the overall cost structure. The front mold accounts for 60% -70% of the total mold cost. By surface treatment (such as nitriding), the depth of the hardened layer is controlled at 0.15-0.25mm, which can ensure the wear resistance of key areas and avoid the processing difficulty caused by high overall hardness. The rear mold is made of materials with lower substrate hardness but better toughness (such as S7 tool steel), which not only meets the impact resistance requirements of the ejector mechanism, but also reduces material procurement costs. A certain household appliance enterprise has reduced the total cost of plastic molds by 18% and extended the maintenance cycle by 30% through this plan.
In special application scenarios, this hardness gradient design is even more important. For example, the front mold of an optical lens needs to be mirror polished to Ra0.01 μ m, and a high hardness substrate can ensure that the polished surface maintains a smoothness of over 90% even after millions of molding cycles. And for large molds for automotive grilles, the high hardness design of the front mold can effectively resist the erosion and wear of fiberglass reinforced materials, increasing the mold repair interval from 50000 mold cycles to 150000 mold cycles.
With the development of simulation technology, hardness optimization has entered the digital stage. Through finite element analysis, the stress distribution under different hardness configurations can be accurately predicted. Based on this, a medical consumables mold enterprise fine tuned the front mold hardness from 50HRC to 48HRC, which extended the mold life by 20% and reduced production energy consumption by 12%. The achievement of this dynamic balance marks the transition of mold design from experience driven to data-driven.