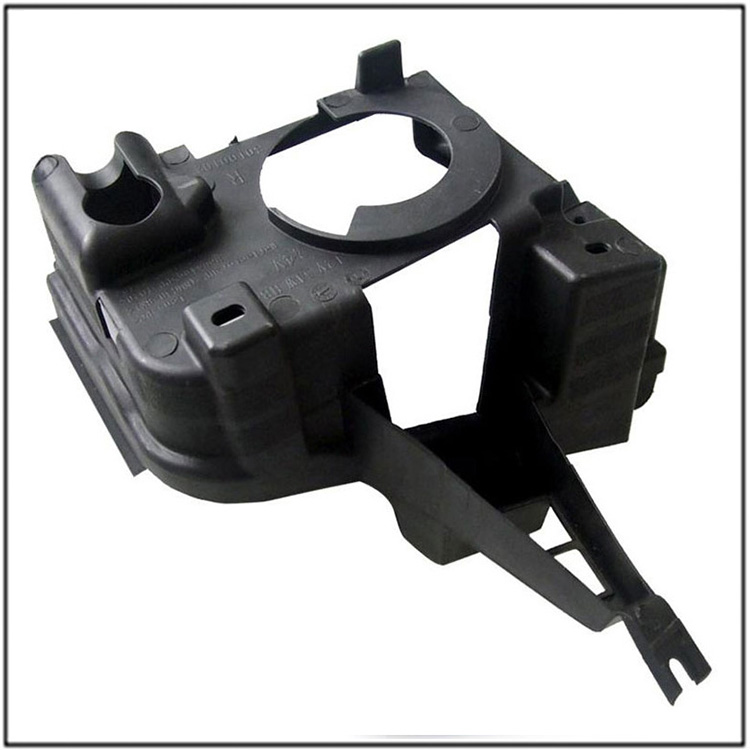
The Properties of Plastic Molds and Alloy Material Molds
In the mold application system of manufacturing industry, plastic molds and alloy material molds represent two completely different technological paths. This difference is not only reflected in the material properties, but also runs through dimensions such as design philosophy, process adaptation, and full lifecycle management, profoundly affecting production efficiency and product quality. Mainly reflected in the following aspects:
1. Materials and Applications
Alloy material mold
-Material: Alloy steel (such as H13, P20) or aluminum alloy is usually used, which has high hardness, high temperature resistance, and wear resistance.
-Usage: Mainly used in metal forming processes (such as die-casting, forging, stamping), such as producing automotive parts, metal shells, etc.
Plastic mold
-Material: mostly made of steel (such as S136, 718) or aluminum alloy, requiring high polishing treatment on the surface.
-Purpose: Specially used for plastic injection molding, production of daily necessities, electronic accessories, packaging containers and other plastic products.
2. Working conditions
-Temperature requirements
-Alloy mold: It needs to withstand extremely high temperatures (such as 600-700 ℃ when die-casting aluminum alloy) and is susceptible to thermal fatigue.
-Plastic mold: The working temperature is relatively low (usually 80-300 ℃), mainly relying on the cooling system to control the temperature.
-Pressure and Wear
-Alloy mold: It needs to resist the high pressure (hundreds to thousands of MPa) and corrosive wear of metal melt.
-Plastic molds: withstand injection pressure (usually 50-150MPa), and wear mainly comes from plastic flow and demolding.
3. Design and Structure
-Flow channel and cooling system
-Alloy mold: Pay attention to the uniformity of metal liquid flow, and the cooling system needs to quickly cool down to prevent defects.
-Plastic mold: The flow channel design needs to optimize the efficiency of plastic filling, and the cooling system directly affects the production cycle.
-Exhaust and surface treatment
-Alloy mold: Efficient exhaust is required to avoid porosity, and the surface is often treated with nitriding to improve adhesion resistance.
-Plastic mold: requires high smoothness (mirror polishing) and relatively simple exhaust design.
4. Lifespan and Cost
-Lifespan
-Alloy molds: Due to high temperature and pressure environments, their lifespan is relatively short (usually tens of thousands to hundreds of thousands of times).
-Plastic molds: have a long lifespan (up to millions of cycles), especially steel molds.
-Cost
-Alloy mold: High material and processing costs, suitable for large-scale production.
-Plastic mold: Aluminum alloy mold has low cost and is suitable for small batches; Steel molds have high cost but long lifespan.
5. Maintenance and repair
-Alloy molds: require regular repair of hot cracks and worn areas, with complex maintenance.
-Plastic molds: Maintenance focuses on cleaning and polishing, and repair is relatively easy.
The properties of alloy material molds and plastic molds are not the same, mainly due to material selection, working environment, design focus, and usage scenarios. Alloy molds are more suitable for high-temperature and high-pressure metal forming, while plastic molds are optimized for plastic characteristics, and there is a clear distinction between the two in terms of technology and process. The correct selection of mold type is crucial for product quality and production efficiency.