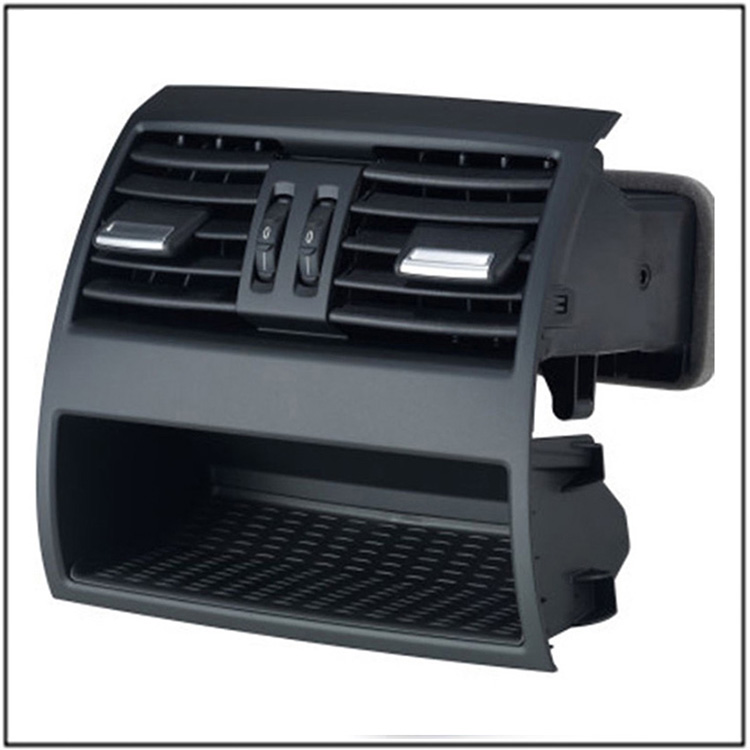
Core Technical of Precision Plastic Molds
In high-end manufacturing fields such as microelectronic connectors and optical lenses, the technical threshold for precision plastic molds has exceeded the micron level precision range. The achievement of this precision is not the result of a single technological breakthrough, but a deep integration of materials science, processing technology, and intelligent control systems, with core requirements covering the entire technology chain from design to production.
The selection of materials forms the basic framework of precision molds. Pre hardened mold steel (such as NAK80) has become the preferred choice for cavity processing due to its crystal uniformity of ≤ 5 μ m. A comparative test of a medical microfluidic chip mold showed that the refined steel using electroslag remelting technology has a 40% reduction in thermal deformation compared to ordinary steel, ensuring a dimensional stability of 0.002mm/m. For optical grade molds, the application of nanoscale precipitation strengthened stainless steel can control the polishing surface roughness within Ra0.01 μ m, meeting the optical surface requirements of products such as blue light readers.
The control system for machining accuracy requires multidimensional technological collaboration. The tool path optimization algorithm of the five axis linkage machining center can compress the profile error of the profile to below 3 μ m. After a certain connector mold enterprise introduced a laser interferometer online compensation system, the verticality deviation of the deep groove structure was improved from 8 μ m to 1.5 μ m. Slow wire cutting uses 0.03mm ultra-fine copper wire combined with intelligent threading technology to achieve a hole position accuracy of ± 1 μ m, which is crucial for miniaturized electronic component molds.
The design of thermal management system directly affects the forming accuracy. The conformal cooling water circuit achieves precise bonding with the mold surface through 3D printing technology, controlling the temperature gradient of the mold within ± 0.5 ℃. Experimental data shows that compared to traditional linear waterways, this design can reduce product warpage by 60%. A certain automotive sensor mold adopts a gradient mold temperature control strategy, maintaining a high temperature of 130 ℃ in the gate area to improve fluidity, and cooling to 80 ℃ in the end area to accelerate shaping. The product weight deviation was successfully reduced from ± 0.15g to ± 0.03g.
The breakthrough progress in surface engineering is reshaping industry standards. The plasma assisted coating technology (PECVD) constructs a diamond-like carbon coating (DLC) on the surface of the mold, with a friction coefficient as low as 0.05, reducing the demolding force of highly transparent materials by 70%. A certain light guide plate production enterprise has extended the mold maintenance cycle from 100000 mold cycles to 500000 mold cycles through this technology, while increasing the product's light transmittance by 3%.
The introduction of intelligent monitoring systems has achieved closed-loop optimization of process control. Embedding fiber optic strain sensors at key positions in the mold can monitor real-time deformation data at the 0.1 μ m level. A certain precision gear mold analyzed these data through machine learning algorithms, dynamically adjusted the locking force and injection speed, and improved the tooth profile accuracy from IT8 level to IT6 level, with a 15% increase in transmission efficiency.
The establishment of a full lifecycle management system is a guarantee of continuous accuracy. The mold health monitoring system based on digital twin technology can predict the wear trend of 0.01mm level. After a connector manufacturer applied this system, the preventive maintenance efficiency increased by 40%, and the product defect rate decreased from 500PPM to 50PPM. This predictive maintenance mode ensures that the accuracy degradation rate of the mold does not exceed 5% within 100000 molding cycles.
Under the background of industrial upgrading, technological innovation in precision plastic molds is extending to interdisciplinary fields. The combination of nanoimprint technology and injection molding process achieves a microstructure replication rate of 99%; The tolerance control of metal powder injection molding (MIM) molds has broken through to ± 0.05mm, opening up a new path for precision medical device manufacturing. These breakthroughs not only drive the precision process of manufacturing, but also create new application possibilities in emerging fields such as 5G communication and genetic testing.