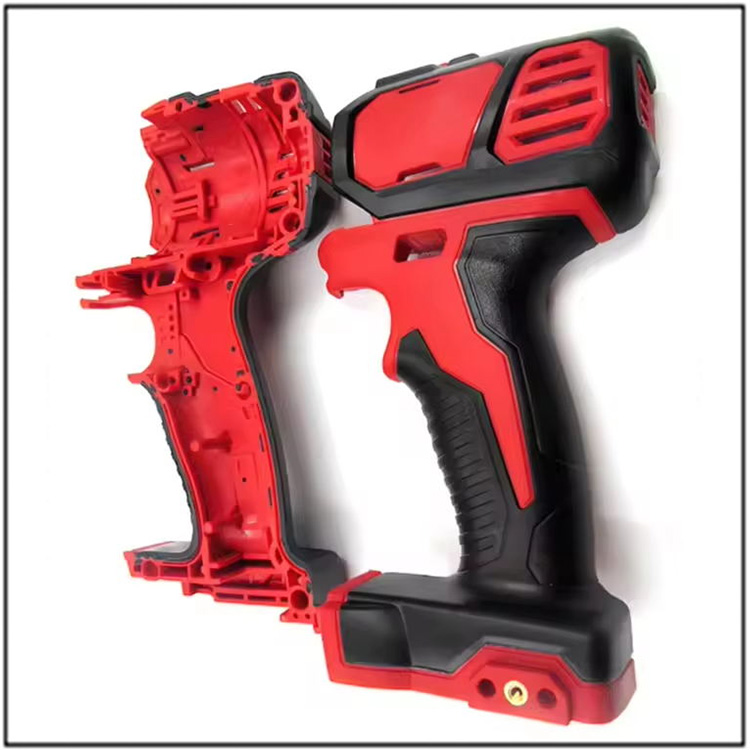
Why is TPU Material Prone to Burrs in Precision Plastic Molds?
TPU (thermoplastic polyurethane) has become an ideal material for products such as seals and sports equipment due to its excellent elasticity and wear resistance. However, during the precision plastic mold forming process, the problem of TPU material producing burrs (flying edges) frequently occurs, directly affecting product yield and production efficiency. Behind this phenomenon lies the complex interaction between material properties and process parameters.
The high elastic modulus of TPU is one of the key factors leading to feathering. Within the processing temperature range of 190-220 ℃, TPU exhibits significant viscoelastic behavior, and its melt easily breaks through the closure limit of the mold parting surface under high pressure. Experimental data shows that the peak cavity pressure of TPU during injection molding can reach 120-150MPa, which is 30-40% higher than that of ordinary ABS. When the parallelism of the mold exceeds 0.02mm, the TPU melt can form visible burrs within 0.3 seconds. A production case of a smart watch wristband shows that after optimizing the accuracy of the mold parting surface, the incidence of burrs is significantly reduced.
The shrinkage characteristics of the material further exacerbate the risk of feathering. The anisotropic shrinkage rate (1.2-1.8%) of TPU during the cooling stage will generate uneven stress. If the mold temperature is not properly controlled, small deformations of 0.05-0.1mm may occur in local areas, weakening the sealing performance of the parting surface. A certain automobile sealing strip manufacturer successfully reduced the defect rate of burrs from 15% to 5% by raising the mold temperature from 40 ℃ to 60 ℃.
Defects in mold design cannot be ignored either. Traditional exhaust systems often struggle to meet the special requirements of TPU: when the exhaust groove depth exceeds 0.015mm, the melt is prone to infiltrate and form a sharp edge. The multi-stage exhaust structure using laser processing (main exhaust groove 0.01mm+auxiliary micropores 5-10 μ m) can improve exhaust efficiency by three times without generating overflow. A medical catheter manufacturing enterprise has solved the long-standing problem of exhaust design optimization.
The setting of process parameters is crucial for edge control. TPU requires a precise injection speed curve: in the initial stage, it breaks through the gate resistance at a medium speed of 30-40%, in the middle stage, it fills the cavity at a high speed of 60-70%, and in the final stage, it compensates for shrinkage at a low speed of 20-30%. A certain sports equipment manufacturer has optimized the three-stage injection process, reducing the defect rate from 12% to below 1%.
The system solution to solve the TPU burrs problem includes: mold reinforcement (using 58-62HRC inserts on the parting surface, TiAlN coating treatment), process optimization (establishing a multidimensional parameter matrix of temperature pressure time), real-time monitoring (dynamically adjusting the locking force), and low-temperature plasma trimming technology. After introducing a machine vision online inspection system, a certain shoe sole manufacturer successfully identified 0.02mm small burrs, reducing the cost of secondary trimming by 70%.
With the development of intelligent technology, TPU Pifeng control is experiencing new breakthroughs. By deeply understanding the interaction between material properties and mold systems, combined with advanced technology and real-time monitoring, the problem of TPU product burrs is gradually being overcome, providing reliable support for precision applications in medical, electronic and other fields. Choosing a mold supplier with proprietary TPU technology experience will be the key to enhancing product competitiveness.